Leakage is caused by improper operation of fittings with cut rings
Jason Gao
2019-06-05 17:06:51
In fact, the jacket pipe joint(fittings with cut ring) has the advantages of simple structure, convenient use and no welding. But in medium and high pressure hydraulic system, improper operation often causes leakage, which affects its popularization and application.
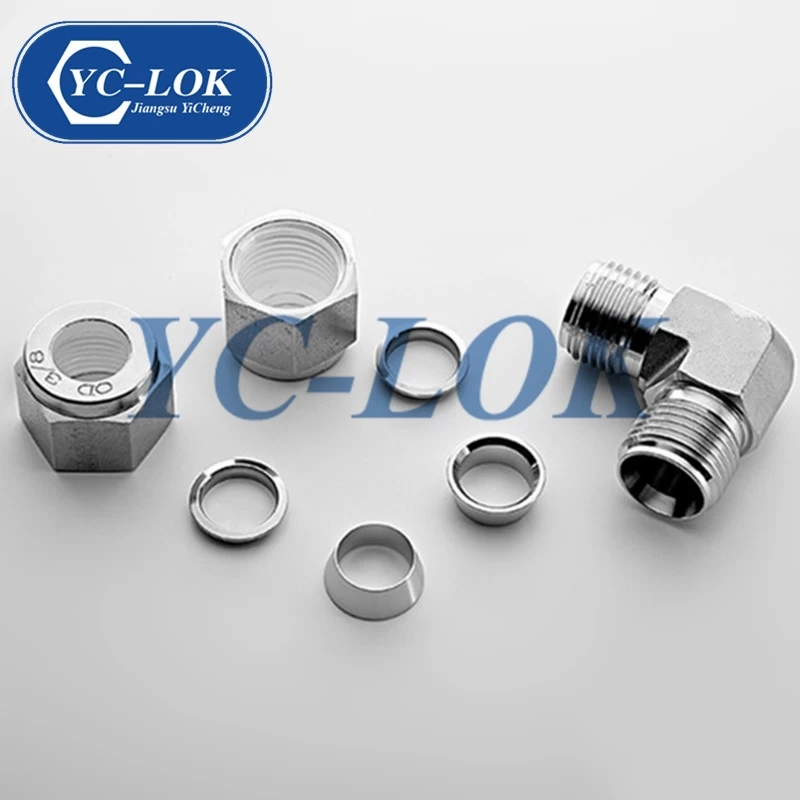
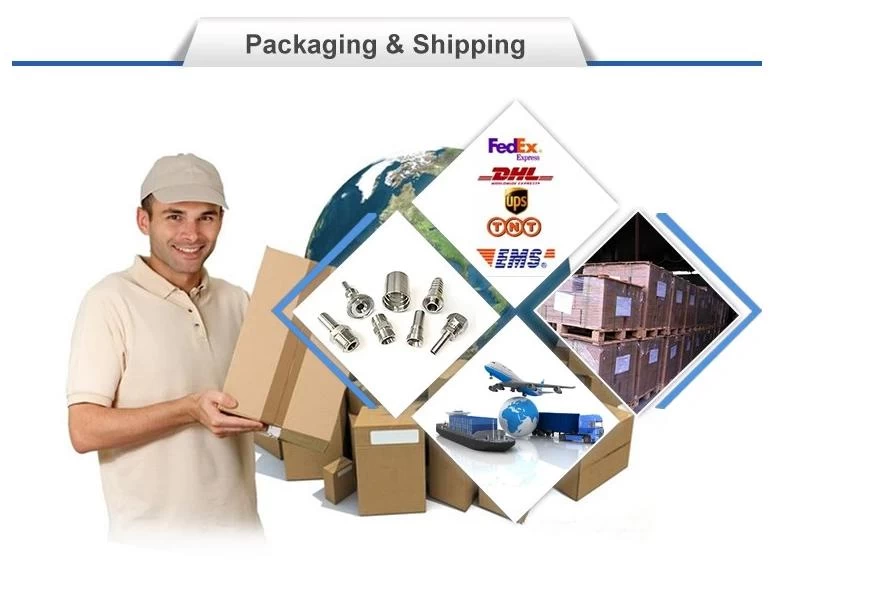
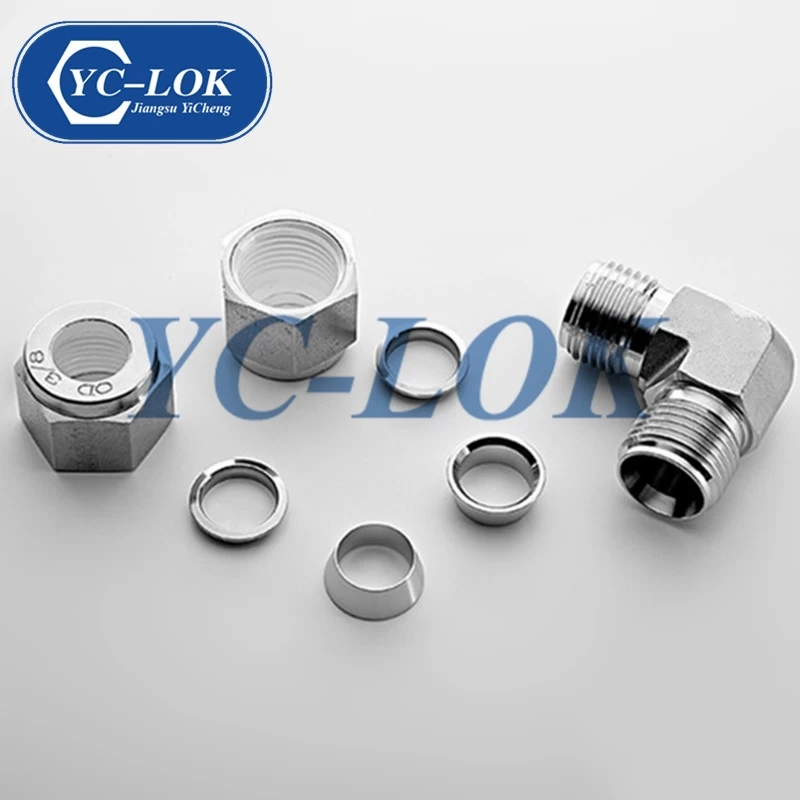
Cautions for jacketed pipe joints: Do not add fillers such as sealant. In order to achieve better sealing effect, some people coated the jacket with sealant. As a result, the sealant was washed into the hydraulic system, resulting in the plugging of the Yinni hole of the hydraulic component and other faults. When connecting pipes, sufficient deformation allowance should be made to avoid the tension of pipes. When connecting the pipeline, it should be avoided to be subjected to lateral force, which will result in improper sealing. When connecting the pipeline, it should be good at one time and avoid multiple disassemblies, otherwise the sealing performance will become worse.
Prefabrication of jacket pipe joints:
Pre-assembly is the most important part of jacketed pipe joint, which directly affects the reliability of sealing. Generally, special preheaters are needed, and fittings with small diameter can be pre-installed on the bench clamp. The main types of jacket type pipe connectors are jacket type straight-through pipe connectors, jacket type end, straight-through pipe connectors and jacket type three-way pipe connectors. Even if the same manufacturer has a batch of goods, the depth of conical holes on these joints is often different, resulting in leakage, and this problem is often ignored. The correct way is, what kind of joint body is used to connect one end of the pipe, and the corresponding joint end is prefabricated with the same type of joint, which can avoid leakage problem to the greatest extent.
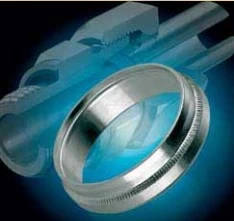
Prefabrication of jacket pipe joints:
Pre-assembly is the most important part of jacketed pipe joint, which directly affects the reliability of sealing. Generally, special preheaters are needed, and fittings with small diameter can be pre-installed on the bench clamp. The main types of jacket type pipe connectors are jacket type straight-through pipe connectors, jacket type end, straight-through pipe connectors and jacket type three-way pipe connectors. Even if the same manufacturer has a batch of goods, the depth of conical holes on these joints is often different, resulting in leakage, and this problem is often ignored. The correct way is, what kind of joint body is used to connect one end of the pipe, and the corresponding joint end is prefabricated with the same type of joint, which can avoid leakage problem to the greatest extent.
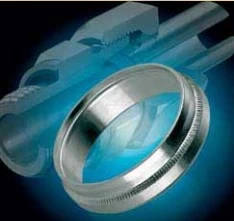
The end face of the pipe should be level. After the pipe is sawed, it should be polished smoothly on tools such as grinding wheels, deburred, cleaned and blown with high-pressure air before use. When preloading, the coaxiality between the pipe and the joint body should be maintained as far as possible. If the pipe deviates too much, the seal will fail. The preloading force should not be too large so that the inner edge of the jacket is just embedded in the outer wall of the pipe, and the jacket should not be obviously deformed. When pipeline connection is carried out, the assembly is carried out according to the prescribed tightening force.
Installation of pipe fittings with jacket type: Pipe pickling should be carried out before pickling is required; Pipe cutting should be done with sawing machine or special pipe cutting machine according to the required length, and no dissolution (such as flame cutting) or grinding wheel cutting should be allowed; round burrs, metal chips and dirt inside and outside pipe ends should be removed; rust inhibitors and dirt of pipe joints should be removed; at the same time, pipe roundness should be guaranteed; Nuts and jackets are inserted into the pipe successively. The front edge (small diameter end) of the jacket is at least 3 mm away from the pipe mouth, and then the pipe is inserted into the cone hole in the joint body until it is crowned. Slowly tighten the nut, while turning the pipe until it is stationary, then tighten the nut 2/3-4/3 turns. Open the jacket to check whether the jacket has been cut into the pipe and whether the position is correct. The clamp sleeve is not allowed to move axially, but can rotate slightly. After checking, the nut is tightened again. Pipe joint
Installation of pipe fittings with jacket type: Pipe pickling should be carried out before pickling is required; Pipe cutting should be done with sawing machine or special pipe cutting machine according to the required length, and no dissolution (such as flame cutting) or grinding wheel cutting should be allowed; round burrs, metal chips and dirt inside and outside pipe ends should be removed; rust inhibitors and dirt of pipe joints should be removed; at the same time, pipe roundness should be guaranteed; Nuts and jackets are inserted into the pipe successively. The front edge (small diameter end) of the jacket is at least 3 mm away from the pipe mouth, and then the pipe is inserted into the cone hole in the joint body until it is crowned. Slowly tighten the nut, while turning the pipe until it is stationary, then tighten the nut 2/3-4/3 turns. Open the jacket to check whether the jacket has been cut into the pipe and whether the position is correct. The clamp sleeve is not allowed to move axially, but can rotate slightly. After checking, the nut is tightened again. Pipe joint
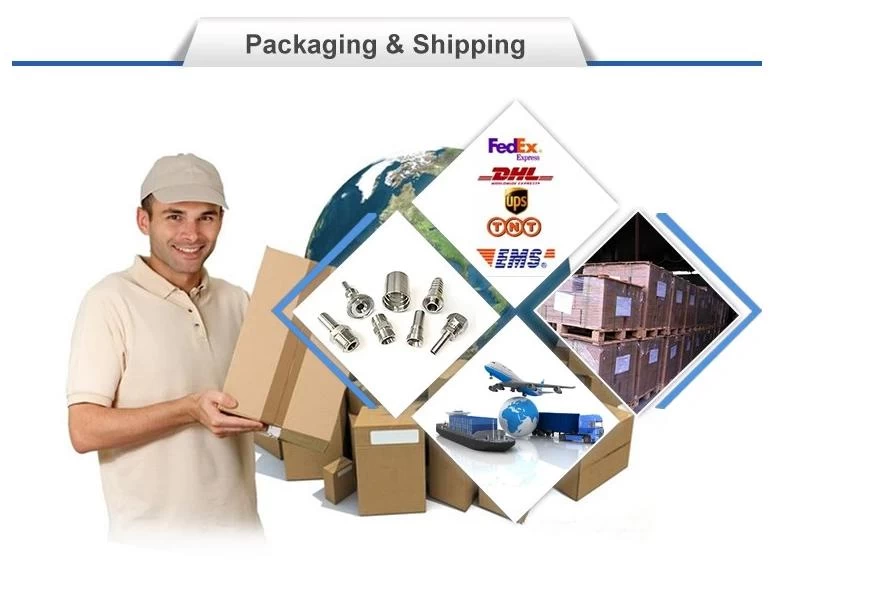